TechnologieN
Schmelzmetallurgische Verfahren
Unsere Kernkompetenz liegt in der Herstellung von Legierungen und Reinmetallen auf Basis der Refraktärmetalle. Die hohe Affinität der Refraktärmetalle zur Atmosphäre erfordert das Schmelzen unter Schutzgas oder im Vakuum. Für diese spezielle Anforderung hat sich GfE ein umfangreiches Portfolio an verschiedenen Technologien erarbeitet. Insbesondere Legierungen auf der Basis von Titan, Vanadium, Chrom, Zirkon, Niob, Tantal sowie die Reinmetalle Titan und Vanadium können wir unseren Kunden anbieten. Hierzu werden folgende Technologien genutzt:
Aluminothermische Reduktion von Oxiden
Der deutsche Chemiker Hans Goldschmidt entwickelte 1895 ein Verfahren, das es ermöglichte, schwer reduzierbare Metalle wie Chrom, Vanadium oder Titan aus deren Oxiden mittels Aluminium kohlenstofffrei zu gewinnen. Diese aluminothermische Reduktion wendet GfE seit mehr als 50 Jahren großtechnisch an. Die Verwendung von Keramiktiegeln erlaubt die hohe Reinheit der erzeugten Metalle und Legierungen. Durch die selbsttätig fortlaufende exotherme Reaktion zwischen Metalloxiden und Aluminium werden Temperaturen bis zu 2.500 °C erreicht. Das schwere Metall sammelt sich dabei am Tiegelboden, das leichtere Aluminiumoxid schwimmt auf dem flüssigen Metall.
GfE produziert nach diesem Verfahren Zwei- und Mehrstofflegierungen, beispielsweise
- Vanadium Aluminium (VAl)
- Nickel Niob (NiNb)
- Ferro Niob (FeNb)
- Molybdän Aluminium (MoAl)
Vakuum-induktionsschmelzen (VIM)
In Gießöfen und Vakuuminduktionsschmelzöfen werden Reinmetalle und Legierungen behandelt, die aufgrund ihrer hohen Affinität zur Luft unter Vakuum oder Schutzgas erschmolzen werden müssen. Die Erschmelzung erfolgt materialspezifisch in Keramik-, Grafit- oder Tongrafittiegeln. Das Metall wird dabei über Mittelfrequenzinduktion erwärmt; das hat zwei wesentliche Vorteile: die Schmelze-Tiegel-Reaktion wird verringert und gleichzeitig das Schmelzgut optimal durchmischt. Die Induktionsschmelztechnik wird auch zur Raffination von Metallen und Legierungen eingesetzt, zum Beispiel zur Entgasung oder Entschlackung.
Mengen- und Materialvarianten
In den Vakuuminduktionsschmelzöfen von GfE können Metalle mit einem Schmelzpunkt von bis zu 1.800°C erschmolzen werden. Dafür stehen unterschiedliche Tiegelvolumina zwischen 10 kg und 2.000 kg Chargengewicht zur Verfügung. Typische Materialien, die mit diesem Verfahren erschmolzen werden, sind unsere Legierungen:
- Aluminium Zinn Zirkon Molybdän Chrom (AlSnZrMoCr)
- Aluminium Niob Silizium Titan (AlNbSiTi)
- Chrom Aluminium (CrAl)
- Silizium Titan (SiTi)
- die Wasserstoffspeicherlegierung (Hydralloy® C)
Zweistufiger Prozess
Als Besonderheit bietet GfE die Möglichkeit, beispielsweise auch Vanadium Aluminium (VAl), Molybdän Aluminium (MoAl) oder Niob Aluminium (NbAl) im sogenannten „zweistufigen Prozess“ herzustellen. Dabei erfolgt im ersten Schritt die aluminothermische Reduktion der Oxide und im zweiten Schritt das Erschmelzen im Vakuuminduktionsofen.
Vakuum-lichtbogenschmelzen (VAR)
Die Herstellung von Ingots aus Titanaluminid erfolgt über einfaches oder mehrfaches Schmelzen von selbstverzehrenden Elektroden mit der jeweiligen Zielzusammensetzung im Vakuumlichtbogenofen (VAR). Ein Teil dieser Ingots wird im VAR Skull Melter erneut aufgeschmolzen, homogenisiert und im Schleudergussverfahren oder Schwerkraftguss zu Formteilen abgegossen. Je nach Anforderung können diese Formteile heißisostatisch zu porenfreien Halbzeugen nachverdichtet (HIP) und zur Einstellung definierter Gefüge wärmebehandelt werden. Auf Kundenwunsch erfolgt eine mechanische Bearbeitung auf Zeichnungsmaß.
Herstellung von Metall- und Raffinationsschmelzen
Im Vakuumlichtbogenofen werden Metalle in einer wassergekühlten Kupferkokille mittels eines energiereichen Lichtbogens erschmolzen. Auf diese Weise werden Verunreinigungen vermieden, die beim Erschmelzen in keramischen- oder Grafittiegeln vorkommen können. Außerdem können so Materialien bis zu einem Schmelzpunkt von 2.200 °C kontrolliert erschmolzen werden. Das ist besonders für Refraktärmetalle wie Zirkon, Titan, Vanadium und deren Legierungen wichtig, da diese Materialien gerne mit nichtmetallischen Materialien reaktionsfreudig reagieren.
Neben der reinen Erschmelzung von Metallen werden bei GfE auch Raffinationsschmelzen durchgeführt. Durch diese spezielle Erschmelzungsart gelingt die Verringerung von leichtflüchtigen Elementen, wie z. B. Natrium, Kalium oder Kalzium. GfE verfügt derzeit über Vakuumlichtbogenöfen mit einem Erschmelzungsvolumen von bis zu 250 kg Chargengewicht.
Typische Legierungen aus dem Vakuumlichtbogenverfahren sind: Titan Aluminium, Titan Zirkon, Titan Niob, Titan Hafnium, Titan Tantal und Niob Titan.
Kaltwand-induktions-tiegelschmelzen (ISM)
Das Erschmelzen von Legierungen in kalten Tiegeln (ISM, Induction Skull Melting) ist eine Sonderform des Vakuum-Induktionsschmelzens und insbesondere geeignet für das Umschmelzen und Homogenisieren von Revert aus Werkstoffen, die sich mit keramischen Tiegeln aufgrund chemischer Reaktionen nicht prozessieren lassen. Hauptanwendung ist das Erschmelzen von werthaltigen Reststoffen aus Titanaluminid-Legierungen und die Herstellung von Halbzeugen mittels Schleuderguss in einem einzigen Fertigungsschritt.
Vakuum-Lichtbogen-Skullschmelzen (VAR SM)
Die meisten der aus dem VAR-Prozess stammenden Ingots werden im VAR Skull Melter als selbstverzehrende Elektroden nochmals aufgeschmolzen. Der hohe Energieeintrag führt dazu, dass das erschmolzene Material im Tiegel im flüssigen Zustand verbleibt und durch die Rührwirkung einer Induktionsspule homogenisiert wird. Mit dem sich anschließenden Schleuderguss oder Schwerkraftguss in metallische Kokillen werden Halbzeuge mit kundengerechten Formen und Abmessungen hergestellt, die sich durch beste Homogenität und geringe Gießporosität aufgrund der Wirkung effektiver Speisersysteme auszeichnen. Die unvermeidbare restliche Gießporosität kann durch ein nachfolgendes heißisostatisches Pressen (HIP) vollständig beseitigt werden.
Pulvermetallurgie- und technologie
Einige Werkstoffe lassen sich schmelzmetallurgisch nicht oder nicht wirtschaftlich herstellen, so dass pulvermetallurgische oder keramische Herstellungstechnologien angewendet werden. Darunter fallen Verbundwerkstoffe, keramische Beschichtungswerkstoffe und Aluminium-Basiswerkstoffe (Aluminium-Titan, Aluminium-Chrom, Aluminium-Silizium).
Atmosphärisches Sintern
In unseren atmosphärischen Sinteröfen werden Refraktärmetalloxide (z. B. Ta2O5, Nb2O5, HfO2, Y2O3/Zr2O3 und ZnO/Al2O3) zu Halbzeugen für die PVD-Beschichtungstechnologie gesintert.
Die Geometrien unserer Beschichtungsmaterialien (z. B. Slugs, Granulate, Kathoden oder Rohre) werden den Beschichtungsanlagen unserer Kunden angepasst. Die Sintertemperaturen können bis zu 1.700 °C betragen.
Hydraulisches Pulverpressen
Dieses Verfahren wird weltweit genutzt, um formstabile Teile aus pulverförmigen Materialien herzustellen.
GfE verfügt über zahlreiche hydraulische Pressen von 15 bis 2.000 t Presskraft, auf denen kleinere Targets aus reinen Metallpulvern (z. B. ZnTiAl-Targets) und Targets aus oxidischen Pulvern (z. B. AZOY (ZnO/Al2O3), TIRU® (TiOx), Ta2O5) gefertigt werden können.
Pulveraufbereitung
Bei der Herstellung von Beschichtungswerkstoffen werden je nach Anforderung verschiedene Pulveraufbereitungstechnologien so kombiniert, dass sie mit den jeweilig verwendeten Rohstoffen optimale Produkteigenschaften gewährleisten. Die Wahl der verwendeten Technologien richtet sich dabei nach dem chemischen Verhalten des eingesetzten Pulvers (Metall oder Oxid), der Korngröße, der Oberflächenbeschaffenheit (Morphologie) und – bei der Herstellung von Pulvermischungen – des jeweiligen Mischungspartners.
Auch die Oberflächenaktivität der Pulver stellt für die Auswahl der geeigneten Technologie ein grundlegendes Entscheidungskriterium dar. Um die Verarbeitung zu erleichtern, werden bei Bedarf Misch- und Kompaktierungshilfsmittel zugesetzt.
Produktspezifisch werden Zerkleinerungs-, Aufbereitungs- und, Klassierungsaggregate sowie Mischvorrichtungen und Granuliereinrichtungen verschiedenster Bauarten eingesetzt.
Vakuum-Schutzgas-Sintern
In unseren Vakuum-Sinteröfen stellen wir Mischoxide und elektrisch leitfähige Suboxide her. Unter genau kontrollierten Bedingungen wird die Ofenatmosphäre so gewählt, dass die besonderen Eigenschaften unserer Produkte erzielt werden können.
So sind wir in der Lage, für die PVD-Beschichtungstechnologie Oxide, Suboxide, Mischoxide und Cermets herzustellen. In unseren Anlagen sind Sintertemperaturen bis zu 2.200 °C erreichbar.
herstellung von Granulaten und pulvern
Mechanisches zerkleinern
Die GfE verfügt über verschiedenste Zerkleinerungs- und Vermahlungsaggregate zur Herstellung von Granulaten und Pulvern. Die Zerkleinerungsaggregate werden speziell für die darzustellende Kornverteilung ausgewählt. Zur Verfügung stehen dabei u. a. abgestimmte Backenbrecher, Walzenbrecher, Hammermühlen, Walzenmühlen, Stiftmühlen und Feinprall-Mühlen. Speziell zur Herstellung feiner Pulver verwenden wir Rohrschwing-Mühlen (Cryopalla-Mühlen), die durch ihren besonderen Aufbau gekühlt werden können. Dies ermöglicht auch das Vermahlen von schwer zerkleinerbarem Material, wie z.B. Titanpulver. Über die verfügbaren Zerkleinerungstechnologien sind Kornfraktionen im weiten Bandbereich 0 bis etwa 80 mm erzielbar.
EIGA Inertgasverdüsung
In der EIGA Verdüsungsanlage (Electrode Induction Gas Atomization) werden homogene Stäbe aus Titan- sowie Titanaluminidlegierungen in einer konischen Spule induktiv abgeschmolzen. Der entstehende Schmelzstrahl wird in einer unter der Induktionsspule liegenden Düse mit Argon zu einem sphärischen Pulver verdüst. Die entstehende Partikelgrößenverteilung kann durch die Variation der Verdüsungsparameter, insbesondere Schmelzrate, Düsendurchmesser und Verdüsungsdruck, beeinflusst werden.
Pulverklassierung durch Sieben
Unabhängig von der Herstellungsart der Pulver entsteht in der Regel ein weites Spektrum an Partikelgrößen, so dass die jeweiligen Nutzfraktionen aus den Pulvern durch Absieben von Unter- und Überkorn gewonnen werden müssen. Hierfür stehen eine Reihe von Vibrations-, Schwing- und Taumelsiebmaschinen zur Verfügung, von denen einige auch unter kontrollierter Schutzgasatmosphäre zur Verhinderung von Sauerstoff- oder Stickstoffaufnahmen der Pulver betrieben werden können. Das Spektrum der Partikelgrößen umfasst einen weiten Bereich von 25 µm bis hin zu einigen Millimetern.
Versprödung von Refraktärmetallen durch Wasserstoff
Herstellung von Titanpulver für die Medizintechnik
Die bei GfE angewandte HDH-Technologie (HDH= Hydrieren-Dehydrieren) ermöglicht das Verspröden zahlreicher Materialien durch die Beaufschlagung mit Wasserstoff. Unter Druck- und Temperatureinwirkung diffundiert der Wasserstoff in das Material und führt in Abhängigkeit seiner Konzentration im Metall zur Versprödung. In diesem Zustand lässt sich das Material zu Pulver vermahlen, bevor es anschließend durch eine Vakuumbehandlung wieder vom Wasserstoff befreit wird. Nach erfolgter Dehydrierung sind nunmehr unterschiedliche Pulverfraktionen nach Kundenwunsch herstellbar.
Thermisches Spritzen
Das Thermische Spritzen ist ein Beschichtungsverfahren, bei dem Spritzzusätze mit hoher thermischer Energie auf eine Bauteiloberfläche aufgeschleudert werden und dort eine Schicht bilden.
Für die Herstellung von thermischen Spritzbeschichtungen wenden wir folgende Verfahren an:
Drahtflammspritzen
Beim Drahtflammspritzen wird der drahtförmige Zusatzwerkstoff durch eine Vorschubeinheit kontinuierlich der Acetylen-Sauerstoff-Flamme zugeführt. Die Drahtvorschubgeschwindigkeit richtet sich dabei nach der Abschmelzleistung des jeweiligen Spritzzusatzes. Das an der Drahtspitze abschmelzende Material wird durch ein Zerstäubergas in Tröpfchen zerteilt, beschleunigt und auf die Werkstückoberfläche geschleudert.
Das Drahtflammspritzen erlaubt je nach Spritzwerkstoff einen hohen Materialdurchsatz mit hohem Auftragswirkungsgrad. So können beispielsweise mit niedriglegierten Stählen kostengünstig mehrere Millimeter dicke Schichten aufgebaut werden.
Erwähnenswert sind Beschichtungen mit Molybdän, das auf Grund seines niedrigen Reibungskoeffizienten und des hohen Widerstandes gegen Kaltverschweißen („Fressen“) besonders für hochbelastete Gleitpaarungen geeignet ist. Ähnliche Anwendungen finden Bronzen oder Weißmetall für Gleitlager.
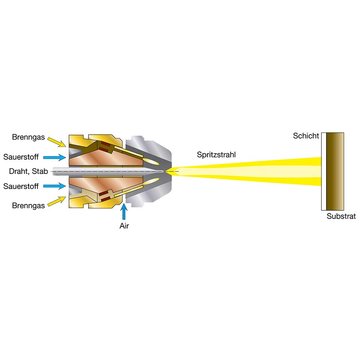
© Oerlikon Metco AG
Unsere Technologie
Unsere robotergeführten Drahtflammspritzpistolen bewähren sich bei vielen metallischen Beschichtungen seit Jahrzehnten.
Ihre Vorteile
- kostengünstiges Verfahren (im Vergleich zur Gussvariante)
- Reparatur von Maschinenteilen möglich
- dicke Aufspritzungen möglich (> 10 mm; werkstoffabhängig)
- Verschleißschutz mit Molybdän möglich
Hochgeschwindigkeitsflammspritzen
Das Hochgeschwindigkeitsflammspritzen (High Velocity Oxygen Fuel, HVOF-Verfahren) ist eine Weiterentwicklung des Pulverflammverfahrens. Die spezielle Brennergestaltung erlaubt Flammgeschwindigkeiten von mehrfacher Schallgeschwindigkeit. Das zugeführte Spritzpulver wird im Vergleich zum Plasmaspritzen dabei weniger erwärmt, dafür umso mehr beschleunigt. Mit Partikelgeschwindigkeiten bis zu 600 m/s entstehen so sehr gut haftende, dichte und homogene Schichten mit typischen Schichtdicken von 0,1–0,4 mm.
Wegen der geringen Schichtporosität ist das HVOF-Verfahren ideal für hoch verschleißfeste Hartmetallschichten aus Wolfram- oder Chromkarbiden, außerdem für korrosionsschützende Metallschichten aus Nickellegierungen oder rostfreien Stählen geeignet.
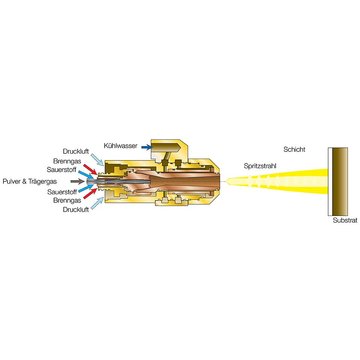
© Oerlikon Metco AG
Unsere Technologie
Mit unserem gasbetriebenen Diamond Jet Hybrid-System sowie dem TopGun-Brenner bieten wir Ihnen zuverlässige Technik für Ihre hochwertigen Produkte.
Ihre Vorteile
- hohe Haftfestigkeit (> 80 MPa nach DIN EN ISO 14916)
- sehr dichte Schichten
- sehr harte Schichten (WC > 1300 HVO,1)
- sehr guter Verschleißschutz
Kaltgasspritzen
Das Kaltgasspritzen ist weniger ein thermisches, sondern eher ein kinetisches Verfahren. Dabei wird ein vorgewärmtes Prozessgas (Stickstoff oder Helium bzw. deren Gemische) unter hohem Druck in einer Lavaldüse entspannt, wobei sich das Gas durch die konvergent-divergente Düsengeometrie auf mehrfache Schallgeschwindigkeit beschleunigt und abkühlt. Der pulverförmige Spritzzusatz wird vor dem Düseneingang in den heißen Prozessgasstrom eindosiert. Die Partikel werden dabei erwärmt und mit dem austretenden Gasstrahl beschleunigt. Je nach Partikelgröße und gewählten Prozessparametern prallen die Teilchen mit Geschwindigkeiten von 500–1000 m/s auf die zu beschichtende Oberfläche auf. Dabei werden die Partikel intensiv plastisch verformt und verbinden sich mit der Bauteiloberfläche und untereinander durch Kaltverschweißung. Die damit erhaltenen Schichten sind praktisch porenfrei und kommen in ihren Eigenschaften dem Massivwerkstoff nahe.
Wegen dieses Grundprinzips sind nur duktile Metalle für das Kaltgasspritzen geeignet. Da die Prozesstemperatur unterhalb der Schmelztemperatur des Spitzwerkstoffes liegt und der Partikelstrahl in einem Inertgasstrom auf das Bauteil trifft, finden keine Phasenumwandlung und Oxidation im Spritzgut statt. Die Reinheit des Ausgangsmaterials bleibt so erhalten. Mit den verfahrenstypischen Druckspannungen in der Spritzschicht sind mehrere Millimeter dicke Schichten möglich.
Typische Applikationen sind lötbare Kupferschichten auf Aluminiumbauteilen wie Kühlkörpern oder Gehäusen. Die Schichten sind mit den Standardlötverfahren der Elektronikindustrie lötbar. Dank der vom Massivwerkstoff wenig abweichenden Schichtqualität sind beispielsweise Reparaturschichten aus Aluminium für hochwertige Luftfahrtbauteile in artgleicher Legierung möglich, die nicht nur fehlendes Material ersetzen, sondern auch dessen Festigkeitseigenschaften übernehmen. Der eng fokussierte Spritzstahl ermöglicht eine endkonturnahe Fertigung auch dreidimensionaler Strukturen.

© Oerlikon Metco AG
Unsere Technologie
Mit unserem Kaltgasspritzsystem Kinetiks 4000 können wir – je nach Ihrer Applikation – eine breite Palette von Werkstoffen verarbeiten, von Aluminium, Kupfer, Zink oder Nickel über Legierungen bis hin zu Tantal und Titan.
Ihre Vorteile
- fest haftende, dichte und metallisch reine Schichten
- selektive Beschichtung, mit Maskierungen und Strukturbreiten < 1mm
- Kupferbeschichtungen in Elektronikqualität
- Schichtdicken von 30 µm bis mehrere mm möglich
- endkonturnahe Strukturen erzeugbar
Lichtbogenspritzen
Beim Lichtbogenspritzen wird wie beim Schweißen ein Lichtbogen zwischen zwei unterschiedlich gepolten Drähten gezündet. Die entstehende Wärme (> 4000 °C) schmilzt die Drahtenden auf; mit einem Zerstäubergas (Luft oder Stickstoff) wird die entstandene Schmelze auf das zu beschichtende Bauteil geschleudert. Durch einen geregelten Drahtvorschub läuft dieser Prozess kontinuierlich ab.
Das Verfahren kombiniert hohen Materialdurchsatz (bis 20 kg/h) mit relativ geringem Energieverbrauch. Es können alle elektrisch leitfähigen Werkstoffe verarbeitet werden, die in Drahtform vorliegen. Sowohl weiche Materialien wie Zinn oder Aluminium als auch harte Eisenbasiswerkstoffe werden eingesetzt. Mit Fülldrähten kommen weitere Komponenten ins Spiel, die als Hartstoffe dienen oder der Schicht Legierungszusätze liefern.
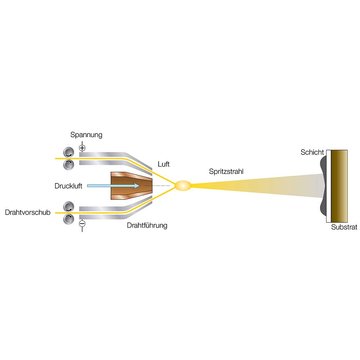
© Oerlikon Metco AG
Unsere Technologie
Mehrere SmartArc-Systeme spritzen bei uns zuverlässig Haftgrund oder Deckschichten aus unterschiedlichen Metallen und Legierungen.
Ihre Vorteile
- effizientes Verfahren
- Thermoplaste beschichtbar (geringe Wärmebelastung des Bauteils)
- breite Palette an metallischen Werkstoffen anwendbar
- Schichtdicken von 0,2–5 mm möglich
- weiche bis harte Schichten (> 60 HRC) möglich
- guter Korrosions- und Oxidationsschutz (Zn, Al)
- für Reparaturen geeignet (Stähle, Nickellegierungen)
- durch Drehen, Fräsen oder Schleifen bearbeitbar
Plasmaspritzen
Atmosphärisches Plasmaspritzen (APS) ist das Verfahren mit der höchsten Prozesstemperatur. Das Plasma wird erzeugt, indem durch einen innerhalb des Plasmabrenners kontinuierlich brennenden Lichtbogen Gase wie Argon, Helium, Stickstoff oder Wasserstoff beziehungsweise deren Gemische strömen. Dabei werden die Gase ionisiert und verlassen den Brenner mit hohen Ausströmgeschwindigkeiten und Temperaturen bis zu 20.000 K. Da diese hohen Temperaturen nur im Bereich der Plasmaflamme wirken, ist die thermische Belastung des Bauteils dennoch gering.
Mit dem APS-Verfahren können hochschmelzende Materialien wie Keramik verarbeitet werden, aber auch Metalle bis hin zu Wolfram. Bevorzugt kommt das Plasmaspritzen zum Einsatz, wenn es um Keramikschichten geht. Aber auch extrem harte und verschleißbeständige Schichten aus Chromoxid für Dichtsitze, Plunger und Walzen, elektrisch isolierende Aluminiumoxidschichten in hoher Reinheit oder hervorragend wärmedämmendes Zirkonoxid sind möglich. Mit entsprechender Komponentenkühlung können selbst Kunststoffe beschichtet werden.
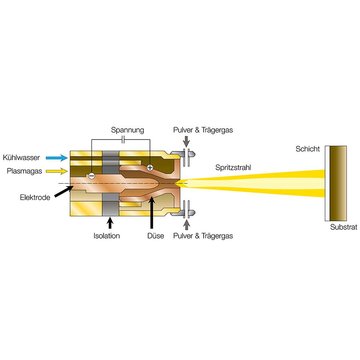
© Oerlikon Metco AG
Unsere Technologie
Mit dem Triplex Pro® Plasmaspritzsystem haben wir die neueste Brennertechnologie für beste Qualität und höchste Leistung.
Ihre Vorteile
- ideal für Keramikschichten
- breite Palette an Beschichtungswerkstoffen
- nahezu alle Grundwerkstoffe beschichtbar
- geringer Wärmeeintrag ins Bauteil (z. B. Beschichtung von Glasrohren)
- Schichtdicken von > 10 µm bis mehrere mm möglich
Pulverflammspritzen
Beim Pulverflammspritzen wird der pulverförmige Spritzwerkstoff in einer Acetylen-Sauerstoff-Flamme an- oder aufgeschmolzen und durch diese auf das vorbereitete Werkstück geschleudert. Beim Erstarren haften die Partikel fest an der Oberfläche und bilden bis zu mehrere Millimeter dicke Schichten. Durch anschließendes Einsintern („Einschmelzen“) können porenfreie, metallurgisch angebundene Schichten erzeugt werden.

© Oerlikon Metco AG
Unsere Technologie
Wir setzen vor allem die ausgereiften, vielseitigen 6P-Brenner ein.
Ihre Vorteile
- kostengünstiges Verfahren
- für Einschmelzlegierungen auf Ni- oder Co-Basis geeignet
- für verschleißfeste Schichten mit hoher Rauheit geeignet
- für Einlaufschichten (Abradables) geeignet
Fertigung von Spezialhalbzeugen
GfE fertigt Spezialhalbzeuge sowohl als Einzelstücke als auch in Klein- oder Großserien. Dabei besteht die Möglichkeit der Lohnumarbeitung des von Ihnen beigestellten Materials. Darüber hinaus bieten wir auch Komplettangebote, wobei wir Rohstoffe in Form von Ingots oder Brammen selbst einkaufen und die Fertigungskette bereits mit Schmelzen und Gießen gestartet werden kann. Über die mechanische Bearbeitung können außerdem fertig einsetzbare Formteile oder Werkstücke nach Zeichnung hergestellt werden.
Folgende Technologien kommen zum Einsatz:
- Schmelzen, Gießen
- Schmieden, Walzen, Hämmern
- Glühen (Hochvakuum, Luft)
- Richten, Schneiden, Stanzen
- Spanende Bearbeitung (Drehen, Fräsen, Schleifen, Polieren)
Mechanisches Bearbeiten der Beschichtungswerkstoffe
Unsere mechanische Bearbeitung ist darauf spezialisiert, nicht umformbare oder schwer zu spanende Materialien zu bearbeiten. Derzeit sind bei GfE mehrere Vertikal- und Horizontalband-Sägemaschinen im Einsatz. Ergänzt wird das Spektrum durch mechanische Bearbeitungszentren, in denen Formteile bearbeitet werden können.
Aufbereitung und Recycling von Vanadium
GfE gewinnt hochreine Vanadium Verbindungen aus Rückständen
Vanadium wird heute noch zu einem großen Teil aus Titanomagnetiterzen und daraus hergestellten Vanadiumschlacken gewonnen. Vanadium fällt auch in Form von petrochemischen Rückständen, Altkatalysatoren, Aschen und Reststoffen an. Das darin enthaltene Vanadium wird in eine wasserlösliche Form gebracht und ausgelaugt. Die so erhaltene Lösung dient als Ausgangspunkt zur Gewinnung von Vanadiumoxiden und Vanadiumsalzen.
GfE hat seit Anfang des zwanzigsten Jahrhunderts in der Gewinnung von hochreinen Vanadium Verbindungen und Vorstoffen zur Herstellung von Vanadiummetall und Vanadium Legierungen wertvolle Erkenntnisse gesammelt. Seit Jahrzehnten entwickelt und produziert GfE diese hochreinen Produkte für unterschiedlichste Anwendungsgebiete in verschiedenen Industriezweigen. Zusätzlich können verbrauchte Katalysatoren innerhalb der AMG-Gruppe verarbeitet werden.Unsere Verfahren zur Gewinnung von Vanadium Verbindungen entlasten die Umwelt. So bleiben Natur und Ressourcen unangetastet.