Technologies
Melting metallurgy procedures
Our core competence is the manufacturing of alloys and pure metals based on refractory metals. The high affinity of refractory metals for the atmosphere requires melting under inert gas or in a vacuum. For this special requirement, GfE has developed an extensive portfolio of different technologies. In particular, we can offer alloys based on titanium, vanadium, chromium, zirconium, niobium, tantalum, and the pure metals titanium and vanadium to our customers. The following technologies are used for this:
Aluminothermic reduction of oxides
In 1895, the German chemist Hans Goldschmidt developed a method that allowed metals that are difficult to reduce, like chromium, vanadium, and titanium, to be extracted from their oxides without carbon, using aluminum. GfE has been using this aluminothermic reduction on a large scale for over 50 years. The use of ceramic crucibles allows the high purity of the metals and alloys created. Due to the automatically continuing exothermic reaction between metal oxides and aluminum, temperatures of up to 2,500 °C can be reached. The heavy metals gather at the bottom of the crucible in this process, and the lighter aluminum oxide floats on the liquid metal.
GfE uses this method to produce binary and multi-material alloys, such as
- vanadium aluminum (VAl)
- nickel niobium (NiNb)
- ferro niobium (FeNb)
- molybdenum aluminum (MoAl)
Cold wall induction skull melting (ISM)
Melting alloys in cold crucibles (ISM, induction skull melting) is a special form of vacuum induction melting, and is particularly well suited for remelting and homogenizing revert from materials that cannot be processed with ceramic crucibles due to chemical reactions. The main application is melting valuable residues from titanium aluminide alloys and manufacturing semi-finished products by means of centrifugal casting in a single production step.
Vacuum arc melting (VAR)
Ingots made from titanium aluminide are manufactured by melting consumable electrodes once or multiple times with the respective target composition in the vacuum arc furnace (VAR). A part of this ingot is remelted in the VAR skull melter, homogenized, and poured out into cast parts in a centrifugal casting process or gravity casting. Depending on the requirements, these cast parts can be hot isostatic pressed (HIP) into non-porous semi-finished products and heat-treated to set specified structures. If requested by the customer, they will be mechanically processed to drawing size.
Manufacturing of molten metals and refinement melting processes
Metals are melted in a water-cooled copper mold inside the vacuum arc furnace using a high-energy electric arc. This method prevents impurities that can occur when melting in ceramic or graphite crucibles. Furthermore, materials can be melted at a melting point of up to 2,200 °C in a controlled manner. This is especially important for refractory metals such as zirconium, titanium, vanadium, and their alloys, as these materials easily become highly reactive with non-metallic materials.
In addition to the pure melting of metals, GfE also performs refinement melting processes. This special type of melting manages to reduce volatile elements such as sodium, potassium, and calcium. GfE currently has vacuum arc furnaces with melting volumes of up to 250 kg batch weight.
Typical alloys from the vacuum arc procedure are: titanium aluminum, titanium zirconium, titanium niobium, titanium hafnium, titanium tantalum and niobium titanium.
Vacuum arc skull melting (VAR SM)
Most of the ingots originating from the VAR process are remelted in the VAR skull melter as consumable electrodes. The high energy input means that the molten material in the crucible remains in a liquid state and is homogenized by the stirring effect of an induction coil. Semi-finished products with customized shapes and dimensions are manufactured with the adjoining centrifugal casting or gravity cast in metallic molds, and are distinguished by the best homogeneity and low casting porosity due to the effect of efficient feeding systems. The unavoidable residual casting porosity can be completely eliminated through a subsequent hot isostatic pressing (HIP).
Vacuum induction melting (VIM)
Pure metals and alloys are treated in casting and vacuum induction melting furnaces if they need to be melted in a vacuum or inert gas due to their high affinity for the air. Depending on the materials, melting is done in ceramic, graphite, or clay graphite crucibles. In this process, the metal is heated by means of medium-frequency induction; there are two major advantages to this. The reaction between the molten mass and the crucible is reduced, and meanwhile the molten metal is thoroughly mixed. The induction melting technique is also used to refine metals and alloys, such as for degasification and purification.
Quantities and material variants
Metals with a melting point of up to 1,800 °C can be melted in GfE’s vacuum induction melting furnaces. Crucibles of various volumes ranging from 10 kg to 2,000 kg batch weight are available for this. Typical materials melted with this method are our alloys:
- aluminum tin zirconium molybdenum chromium (AlSnZrMoCr)
- aluminum niobium silicon titanium (AlNbSiTi)
- chromium aluminum (CrAl)
- silicon titanium (SiTi)
- the hydrogen storage alloy (Hydralloy® C)
Two-step process
As a special feature, GfE also offers the option to manufacture alloys such as vanadium aluminum (VAl), molybdenum aluminum (MoAl), and niobium aluminum (NbAl) in a two-step process. The first step is aluminothermic reduction of oxide, and the second step is melting in the vacuum induction furnace.
Powder metallurgy and technology
Some materials cannot be manufactured through melting metallurgy, or it cannot be done economically, and so powder metallurgical or ceramic manufacturing technologies are applied. These include composites, ceramic coating materials, and aluminum-based materials (aluminum titanium, aluminum chromium, aluminum silicon).
Atmospheric sintering
In our atmospheric sintering furnaces, refractory metal oxides (such as Ta2O5, Nb2O5, HfO2, Y2O3/Zr2O3, and ZnO/Al2O3) are sintered into semi-finished products for the PVD coating technology.
The geometries of our coating materials (e.g. slugs, granules, cathodes, and tubes) are adapted for the coating systems of our customers. Sintering temperatures can be up to 1,700 °C.
Hydraulic powder Compression
This method is used around the world for manufacturing dimensionally stable parts from powdery materials.
GfE has a number of hydraulic presses ranging from 15 to 2,000 tons of pressing force, on which smaller targets made from pure metal powders (e.g. ZnTiAl targets) and targets made from oxidic powders (e.g. AZOY (ZnO/Al2O3), TIRU® (TiOx), Ta2O5) can be manufactured.
Powder preparation
In manufacturing coating materials, different powder preparation technologies are combined depending on the requirements to guarantee the best product properties with the respective raw materials used. The choice of technologies used is based on the chemical behavior of the powder used (metal or oxide), grain size, surface quality (morphology), and – for manufacturing powder mixtures – the respective mixing partner.
The surface activity of the powder also represents an essential deciding factor for choosing the right technology. To make processing easier, mixing and compacting agents are added as needed.
Crushing equipment, preparation and classing aggregates, mixing devices, and granulation equipment of all different kinds are used depending on the specific product.
Vacuum inert gas sintering
We manufacture mixed oxide and electrically conductive suboxides in our vacuum sintering furnaces. The furnace atmosphere is selected under carefully controlled conditions so that the special properties of our products can be attained.
This makes it possible for us to manufacture oxides, suboxides, mixed oxides, and cermets for PVD coating technology. Sintering temperatures of up to 2,200 °C can be reached in our systems.
powder and granulate manufacturing
Mechanical crushing
GfE has a wide variety of crushing and grinding machines for manufacturing powders and granulates. The crushing machines are specifically chosen for the particle size distribution to be achieved. Some of those available include jaw crushers, gyratory crushers, roll crushers, roller mills, pin mills, and fine impact mills. For manufacturing fine powders, we use vibration tube mills (Cryopalla mills) that can be cooled due to their special design. This also makes it possible to pulverize materials that are hard to crush, such as titanium powder. Grain fractions in the wide band range 0 to approx. 80 mm can be achieved by means of the available crushing technologies.
EIGA inert gas atomization
In the EIGA atomization system (Electrode Induction Gas Atomization), homogeneous rods made from titanium and titanium aluminide alloys are inductively melted into conical coils. The melted stream that results is atomized into a spherical powder in a nozzle with argon underneath the induction coil. The resulting particle size distribution can be impacted by variations in the atomization parameters, particularly the melting rate, nozzle diameter, and atomization pressure.
Powder classifying through sieves
Regardless of the type of manufacture, the powder is generally formed in a wide spectrum of particle sizes, so the respective usage fractions of the powders need to be obtained by sieving undersize and oversize particles. A range of vibration- , oscillating- and tumbler screening machines are available for this, some of which can also be operated under controlled inert gas atmospheres to prevent the powder from taking in oxygen or nitrogen. The spectrum of particle sizes covers a wide range from 25 µm to a couple millimeters.
Embrittlement of refractory metals with hydrogen
Manufacturing titanium powder for medical technology
The HDH technology used at GfE (HDH=Hydride-Dehydride) allows a number of materials to be embrittled through the application of hydrogen. Under the effects of pressure and temperature, the hydrogen diffuses into the material and, depending on its concentration in the metal, causes the embrittlement. In this condition, the metal can be ground into powder before it is then relieved of hydrogen again by means of a vacuum treatment. After successful dehydration, various powder fractions can now be manufactured as desired by the customer.
Thermal spraying
Thermal Spraying is a coating method in which spray mixtures with high thermal energy are spin-coated onto a component surface, and form a layer there.
For the manufacturing of thermal spray coatings, we use the following methods:
Arc spraying
Similar to welding, arc spraying involves igniting an electric arc between two wires with opposing poles. The heat that forms (> 4000 °C) fuses the ends of the wires; with an atomizing gas (air or nitrogen), the molten mass formed is spun onto the component to be coated. This process runs continuously through a controlled wire feed.
The procedure combines high material flow rate (up to 20 kg/h_ with relatively low energy consumption. All electrically conductive materials in wire form can be processed. Both soft materials like tin and aluminum and hard iron-based materials are used. With flux-cored wire, other components come into play that serve as hard materials or provide alloy additions to the layer.
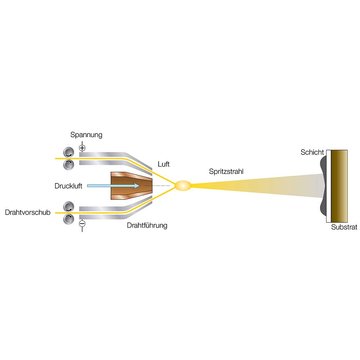
© Oerlikon Metco AG
Our technology
We use several SmartArc systems to reliably spray adhesive primers and top layers made from metals and alloys.
Your advantages
- efficient procedure
- coatable thermoplastics (low heat exposure for component)
- wide range of metallic materials can be used
- layers can be 0.2–5 mm thick
- soft to hard layers (> 60 HRC) possible
- good corrosion and oxidation prevention (Zn, Al)
- suitable for repairs (steels, nickel alloys)
- can be treated by turning, milling, or grinding
Cold gas spraying
Cold spraying is less of a thermal and more of a kinetic method. It entails decompressing a preheated process gas (nitrogen or helium or a mixture of those) under high pressure in a de Laval nozzle, whereby the gas is accelerated to several times the speed of sound and cooled due to the converging-diverging nozzle geometry. The powder-shaped spray filler is dispensed into the hot flow of process gas before the nozzle inlet. The particles are heated and accelerated with the stream of gas that escapes. Depending on the particle size and the process parameters selected, the particles will hit the surface to be coated at a speed of 500–1000 m/s. The particles then undergo intensive plastic deformation, and bond with the component surface and each other due to galling. The layers obtained by this are practically non-porous and come very close to solid material in their properties.
Due to this underlying principle, only ductile metals are suitable for cold spraying. Because the process temperature is below the melting temperature of the spray material and the particle stream enters an inert gas stream on the component, there is no phase transformation or oxidation in the spray material. Thus the purity of the raw material is preserved. With the compression stresses in the spray layer typical of the procedure, the layers can be several millimeters thick.
Typical applications include solderable copper layers on aluminum components such as heat sinks and housing. The layers can be soldered using standard soldering methods in the electronics industry. Thanks to the layer quality that differs little from solid material, aluminum repair layers for high-quality aircraft components of the same type alloy, which not only replace missing material, but also take on its solid qualities. The narrow stream of spray allows even three-dimensional structures to be manufactured close to their final contours.

© Oerlikon Metco AG
Our technology
With our cold gas spray system Kinetiks 4000, we can – depending on your application – process a wide range of materials, from aluminum, copper, zinc, and nickel to alloys, tantalum, and titanium.
Your advantages
- highly adhesive, dense, and metallically pure layers
- selective coating, with masking and structure widths < 1mm
- Electronic-grade copper coatings
- layer thicknesses from 30 µm to several millimeters
- can create structures close to final contours
High velocity flame spraying (HVOF)
High velocity flame spraying (high velocity oxygen fuel, HVOF procedure) is another development in powder flame methods. The special design of the burner allows flame speeds several times the speed of sound. The spray powder fed in is not heated as much in the process in comparison to plasma spraying, but is accelerated more. With particle speeds of up to 600 m/s, thick, homogenous layers with excellent adhesive properties form, typically 0.1–0.4 mm thick.
Due to the low porosity of the layers, the HVOF method is ideal for highly wear-resistant hard metal layers made from tungsten or chromium carbides, and is suitable for corrosion-resistant metal layers made from nickel alloys or stainless steels.
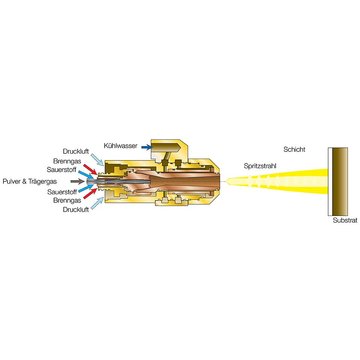
© Oerlikon Metco AG
Our technology
With our gas-powered Diamond Jet Hybrid System and the TopGun burner, we offer you reliable technology for your high-quality products.
Your advantages
- high adhesive strength (> 80 MPa in accordance with DIN EN ISO 14916)
- extremely thick layers
- extremely hard layers (WC > 1300 HVO,1)
- excellent wear resistance
Plasma spraying
Atmospheric Plasmaspraying (APS) is the method with the highest process temperature. The plasma is generated by streaming gases (argon, helium, nitrogen, hydrogen, or a mix of these) through a continuously burning electric arc inside a plasma burner. In this process, the gases are ionized and leave the burner at high outflow velocity and temperatures up to 20,000 K. Because these high temperatures are only active around the plasma flame, the component’s thermal exposure is still low.
The APS method can be used to process high-melting materials like ceramic, or metals including tungsten. Plasma spraying is the preferred method for ceramic layers. However, it can also be used for extremely hard, wear-resistant layers made from chromium oxide for tight seals, plungers, and rollers, electrically insulating aluminum oxide layers with high purity or with excellent heat insulating properties. With the right component cooling, even plastics can be coated.
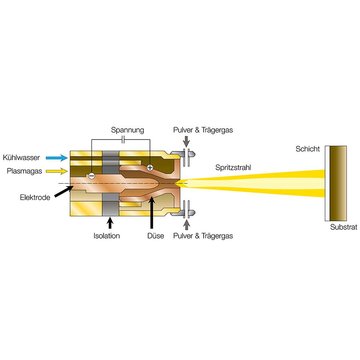
© Oerlikon Metco AG
Our technology
With the Triplex Pro® plasma spraying system, we have the latest burner technology for the best quality and performance.
Your advantages
- Ideal for ceramic layers
- wide range of coating materials
- nearly all base materials can be coated
- low heat input into component (e.g. coating glass tubes)
- layers of > 10 µm can be several millimeters thick
Powder flame spraying
Powder flame spraying entails melting or fusing the spray material in powder form in an oxyacetylene flame and spinning it onto the prepared workpiece. When it solidifies, the particles adhere to the surface and form layers up to several millimeters thick. The subsequent sintering in (fusing) can create non-porous layers attached by metallurgy.

© Oerlikon Metco AG
Our technology
We primarily use the sophisticated, versatile 6P burner.
Your advantages
- cost-effective procedure
- suitable for Ni- or Co-based self-fluxing alloys
- suitable for wear-resistant layers with high roughness
- suitable for abradables
Wire flame spraying
Wire flame spraying entails feeding wire-shaped filler material continuously through a feed unit into the oxyacetylene flame. The speed at which the wire is fed through in this process is based on the deposition rate of the respective spray filler. The melting material on the wire tips is split into droplets by an atomizing gas, accelerated, and spun onto the tool surface.
Depending on the spray material, wire flame spraying allows for a high material flow rate with high transfer efficiency. In this way, for example, low-alloyed steels can be used to build up layers several millimeters thick at low cost.
Worth mentioning are coatings with molybdenum, which is particularly suitable for tribological pairings exposed to high stress due to its low friction coefficient the high resistance to galling (“fretting”). Bronze and white metal have similar applications for bearings.
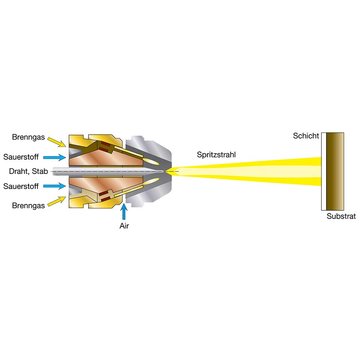
© Oerlikon Metco AG
Our technology
Our robot-guided wire flame spraying guns have proven successful in many metallic coatings performed over decades.
Your advantages
- cost-effective method (compared to casting alternatives)
- machine parts can be repaired
- thick spray coatings possible (> 10 mm; depending on material)
- wear resistance possible with molybdenum
Manufacturing special semi-finished products
GfE manufactures special semi-finished products as both individual parts and small and large batches. This process includes the option for contract reprocessing of material provided by you. In addition, we also offer full packages in which we sell the raw materials ourselves in the form of ingots or slabs, and the production chain can be started as early as the melting and casting process. Mechanical processing can also be used to manufacture ready-to-use molded parts or tools according to drawings.
The following technologies are used:
- melting, casting
- forging, rolling, hammering
- annealing (high vacuum, air)
- leveling, cutting, stamping
- machining (turning, milling, grinding, polishing)
Mechanical processing of coating materials
Our mechanical processing specializes in materials that are not malleable or are difficult to machine. GfE currently uses several vertical and horizontal bandsaw machines. The range is completed by mechanical processing centers where molded parts can be processed.
Preparing and recycling vanadium
GfE extracts high-pure vanadium compounds from residues
Today, the majority of vanadium is still extracted from titanium magnetite ores and the resulting vanadium slag. Vanadium occurs also in the form of petrochemical residues, old catalysts, ashes, and waste material. The vanadium contained within is brought to a water-soluble state and leached out. The solution obtained in this way serves as a starting point for extracting vanadium oxides and vanadium salts.
Since the beginning of the 20th century, GfE has been gathering valuable knowledge on the extraction of ultrapure vanadium compounds and raw materials for manufacturing vanadium metal and alloys. GfE has spent decades developing and producing these high-pure products for highly diverse areas of application in various industry branches. Furthermore, used catalysts can be processed within the AMG group. Our methods for extracting vanadium compounds are easy on the environment. Nature and resources are left untouched.