thermal Spray
YOUR DEVELOPMENT PARTNER FOR FUNCTIONAL LAYERS
GfE has been a pioneer in thermal spraying since the 1980's. What could only be applied by hand-operated spray guns a hundred years ago is now done by spray robots in computerized plants. Mastering thermal spraying techniques and expanding the limits of their applications require scientific and technical methods along with experienced development engineers, technicians, and plant operators.
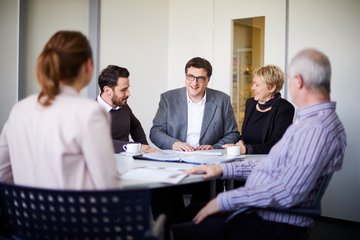
Innovative as a Team
Our engineers and technicians develop functional layers for our customers’ components and implement these from the prototype to series production. We define the required technologies, including the appropriate measuring and testing procedures, together with our customers from the very start. GfE relies on its formula for success: Years of expertise combined with technical achievements lead to long-term results
"In addition to in-depth consulting, short delevery times, and outstandig quality, we offer our customers on thing above all: custom solutions tailored to their needs."
proven in application
GfE has extensive application experience in thermal spraying procedures, the pre- and post-processing of customer parts, and the development of specific production processes for serial coating. The tests, parameter optimizations, and sample coatings required for application development are performed on production equipment under industrial conditions, which makes it easier to rapidly implement the development results in industrial manufacturing.
new developments
New product ideas often require fundamental technology developments with the corresponding trials, tests, material analyses, and material tests. This is also where the decades-long experience of our accredited laboratory for metallography and material testing and the laboratory for chemical analytics come into play.
"Together, our team will find a solution, even for highly specific queries".
thinking towards to the future
Innovative thinking is extremely important to GfE – in all directions and in all areas. This could mean tapping into new fields of application for thermal spraying, such as electromobility. There are new ways of organizing production and new forms of overall technology – higher series volumes inevitably lead to high levels of automation with completely new requirements for plant engineering. But increasingly, there are also new properties of coatings due to the combination and integration into multilayer systems, precision processing with lasers, etc., and new spray technology that can process suspensions.
We maintain regular technical exchanges with external research institutions, such as Fraunhofer-Gesellschaft or technical universities, often about joint development projects.
current layer developments
Below, we would like to give you a brief idea of the developments that have significantly enhanced the applications of thermal spray coatings in recent years.
Digital heating by means of multilayers
Excerpt from GTS-Strahl, 01/2022 ...
...A relatively new application example of precisely manufactured high-performance coatings is a thermally sprayed multi-layer system such as i-CER+. The thermally sprayed surface heaters created by this method can be applied on planar as well as cylindrical components. Due to the low thermal masses and compact design without insulating gaps, the heating and cooling behavior is highly dynamic. With high supply voltages, it takes only fractions of seconds to reach temperatures of several hundred °C. The thermocyclic stress on the heat-conducting layer can be very high during operation. This is why there are particularly high requirements for the quality of the layer application ...
High, stable friction coefficients thanks to ceramic coating
Excerpt from GTS-Strahl, 01/2022 ...
...With f-CER®, GfE has established a combination of layer materials (ceramic components) and coating process (by means of APS) that significantly increases the friction coefficient for force-fitted steel-steel pairings and which remains stable even in the event of multiple assemblies/disassemblies and an overload of the coupling. While a steel-steel pairing is usually designed with a static friction coefficient of µ = 0.12, systems using f-CER® achieve values between µ = 0.5 and 0.9, including under oiled conditions. This makes it possible to reduce the installation space and mass. In addition to the high stress on the layer, there are also stringent requirements regarding the layer thickness, layer form, and layer position tolerances. With f-CER®, it is possible to permanently achieve layer thickness tolerances of +/- 10 µm ...
Our customers determine the flow direction
The special technological aspects of thermal spraying when applying relatively large particles on component surfaces lead to the usual specific microstructure of the sprayed layer with a certain residual porosity and cracking. What may be considered a “flaw” at first glance through a microscope is actually an advantage in many applications and is purposefully utilized. This is the case with heat-insulating layers in the turbine area, for example, where the precisely integrated microstructure with a high pore content makes the function possible in the first place. This significantly improves the thermal insulation of the coating material, for example, zirconium oxide, also enabling firm layer adhesion on the metallic base material, even at operating temperatures far above 1,000 °C.
With p-MET and p-CER, GfE Fremat has developed a layer system for machine and system components that features not only the usual functionalities, but also enables defined and finely distributed gas flows with uniform surfaces. These can be used in both directions: either to generate underpressure for holding loose objects on surfaces or flexible web material on rollers, or for also creating gas cushions under these materials. Differently shaped base bodies can be coated with p-MET and p-CER. These can be parts with planar surfaces, as well as cylindrical, spherical, or tapered shafts. Depending on the further requirements, metallic alloys such as stainless steel or oxide-ceramic compounds, such as zirconium oxide, can be used.
Sustainable mobility through cold spraying
Since the industrial availability of cold spraying systems in Europe almost 20 years ago, copper coatings of aluminum base bodies have played an increasingly important role. Due to their high thermal conductivity, good solderability, good adhesion on aluminum, easy applicability of precise selective coatings and other advantages, cold-sprayed copper layers are the ideal link between power electronics and the respective base bodies (heat sinks, baseplates, housings, and more).
c-MET coatings by GfE have already proven themselves in hybrid and electric vehicles for many years. GfE engineers and technicians are already contributing to the series development of automotive suppliers, from the design and sample phases, to series production. In addition to the series capability of c-MET cold spraying, our team has also developed and optimized peripheral processes, such as incoming inspections, cleaning, quality tests, and packaging, in accordance with customer specifications.
The limits of joinability - Project CHIMERA
GfE Fremat is currently working on optimizing the coating of plastics and composites, especially for EMC and structural applications. In cooperation with partners in industry and research in the joint CHIMERA project, for example, entirely new technological strategies for the coating of lightweight construction materials are being explored and developed. Although thermal spray coatings of plastics, fiber-reinforced plastics, and other lightweight construction materials are already being applied in industrial practice, the insufficient alternating stress resistance of the coatings, along with inadequate safety, are some of the factors hindering large-scale technical applications. The plan is to advance the further functionalization of lightweight construction materials by means of specific surface structuring before the coating process, parameter optimizations of the coating processes themselves, and other steps. You can find more information about this on the project page: Functionalization of laser-structured fiber-plastic-composites through thermal spraying (CHIMERA) - Fraunhofer IWS